Digital signage displays are increasingly essential in industries like retail, hospitality, and corporate environments, where they serve as powerful tools for advertising, information sharing, and customer engagement. However, shipping these large, fragile, and often expensive items presents unique challenges that require careful planning and execution. From their sheer size and weight to their delicate screens and the regulatory hurdles involved, transporting digital signage displays demands a strategic approach to ensure they arrive at their destination in perfect condition.
In this article, we’ll explore the key challenges of shipping digital signage displays and provide practical solutions to help businesses protect their investments and maintain customer satisfaction.
Challenges in Shipping Digital Signage Displays
1. Size and Weight
Digital signage displays, especially video walls and large LED panels, can be massive in both size and weight. A single unit might measure several feet in width and height and weigh hundreds of pounds, making it difficult to handle and transport. For example, a large video wall display could measure 10 feet by 6 feet and weigh over 500 pounds, requiring specialized equipment like forklifts or lift gates for loading and unloading. Additionally, their size often necessitates specific shipping vehicles, such as flatbed trucks, and compliance with transportation regulations regarding oversized loads. Finding the right carrier and ensuring the shipment adheres to weight and dimension limits can be a significant hurdle.
2. Fragility
The screens of digital signage displays, typically made of LCD or OLED materials, are highly susceptible to damage. Even a minor impact, vibration, or temperature fluctuation during transit can crack the screen or harm internal components, rendering the display unusable. A single drop or jolt can lead to costly repairs or replacements, making fragility one of the most critical concerns when shipping these items. The delicate nature of these displays requires extra precautions in packaging and handling to prevent damage.
3. Regulatory Compliance
Shipping large electronic items like digital signage displays may involve navigating a complex web of regulations. For instance, if the display contains lithium batteries, it could be classified as hazardous material, requiring specific labeling, packaging, and documentation under U.S. Department of Transportation (DOT) guidelines.
4. Logistical Challenges
Coordinating the pickup, transportation, and delivery of digital signage displays can be logistically demanding, especially when multiple units are involved or when tight deadlines must be met. For example, a retail chain deploying displays across several locations may face challenges in synchronizing deliveries, managing documentation, and ensuring timely installations for marketing campaigns. International shipments add another layer of complexity, involving customs clearance, duties, and coordination with multiple carriers. Without meticulous planning, these logistical hurdles can lead to delays, increased costs, or damaged goods.
Solutions for Safe Transportation
1. Use Custom-Sized Crates or Pallets
To address the size and weight challenges, it’s essential to use custom-built crates or pallets that are tailored to the exact dimensions of the display. A well-fitted crate ensures a snug fit, minimizing movement during transit and reducing the risk of damage. For example, a custom wooden crate with foam inserts can provide both structural support and cushioning. This approach also simplifies loading and unloading, as the crate can be designed to accommodate forklifts or other handling equipment. Partnering with freight carriers experienced in handling oversized items is equally important, as they can provide the necessary vehicles and expertise.
2. Incorporate Protective Padding and Cushioning
Protecting the fragile screens of digital signage displays requires multiple layers of defense. Use foam padding, bubble wrap, or air pillows to cushion the display and absorb shocks during transit. For added protection, consider double-boxing the display: place it in a smaller box with cushioning, then place that box inside a larger crate with additional padding. Clearly label the package as “Fragile” and use arrows to indicate the correct orientation. These materials and techniques are proven to safeguard electronics during shipping.
3. Utilize Specialized Freight Carriers and Tracking Systems
Partnering with freight carriers that specialize in transporting delicate electronics is crucial. These carriers offer services tailored to high-value or fragile items, including real-time tracking, temperature control, and insurance options. Additionally, implement advanced tracking systems to monitor the shipment’s location and condition throughout transit.
See Your Shipment’s Journey with Freight SideKick’s Tracking Map
Once your shipment is on the move, Freight SideKick’s tracking map gives you a clear, real-time view of its journey—whether it’s a multi-stop route or a single delivery. Our GPS tracking is enabled by default for all truckloads and most other non-LTL shipments, so you can monitor your freight’s progress with ease.
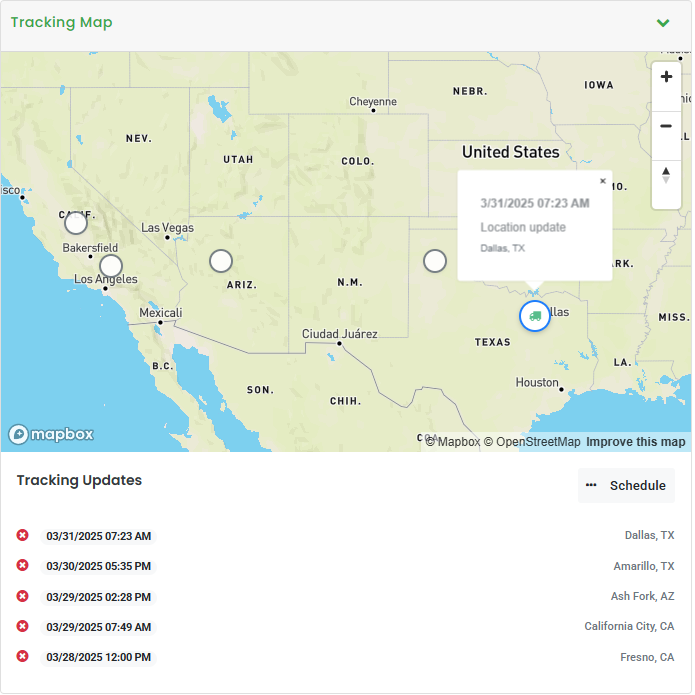
Conclusion
Shipping digital signage displays requires meticulous attention to detail due to their size, fragility, and the regulatory and logistical challenges involved. By using custom packaging, incorporating protective cushioning, ensuring regulatory compliance, and leveraging specialized carriers and tracking systems, businesses can significantly reduce the risk of damage and ensure a smooth shipping process. These steps not only protect valuable investments but also help maintain customer satisfaction by delivering displays in perfect condition.
Get Personalized Assistance
Get a quote today, call 877-345-3838, or email us at support@freightsidekick.com.